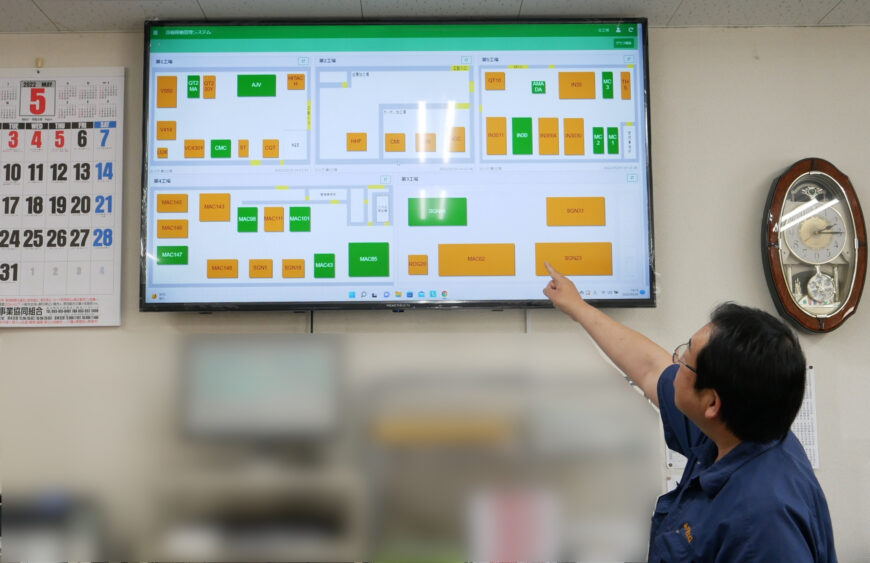
「複合品、特殊品のコンビニ工場!」と自らを名乗る山下機工株式会社。
金属、セラミック、カーボンの3種の素材を扱い、1種類でも、小ロットのオーダーでも、複雑な形状の部品でも仕事を受けるという柔軟な対応が自慢の工場です。
それを可能にしているのが24時間365日稼働可能な交代制勤務の製造体制と、時代を見極めながら新しいものにチャレンジしていく創業魂。2024年で創業100年を迎える老舗企業ですが、なんと、現在「第4の創業」を推進中!
主に半導体製造装置、液晶製造装置、工作機械、食品製造装置などの部品製作に特化していますが、こういった多種多様な部品製作をする上で、常に機械の稼働状況を把握することが重要となり、電圧による稼働管理システムの導入を開始。現在に至るまでの経緯を担当の秋山哲史さんにお伺いました。
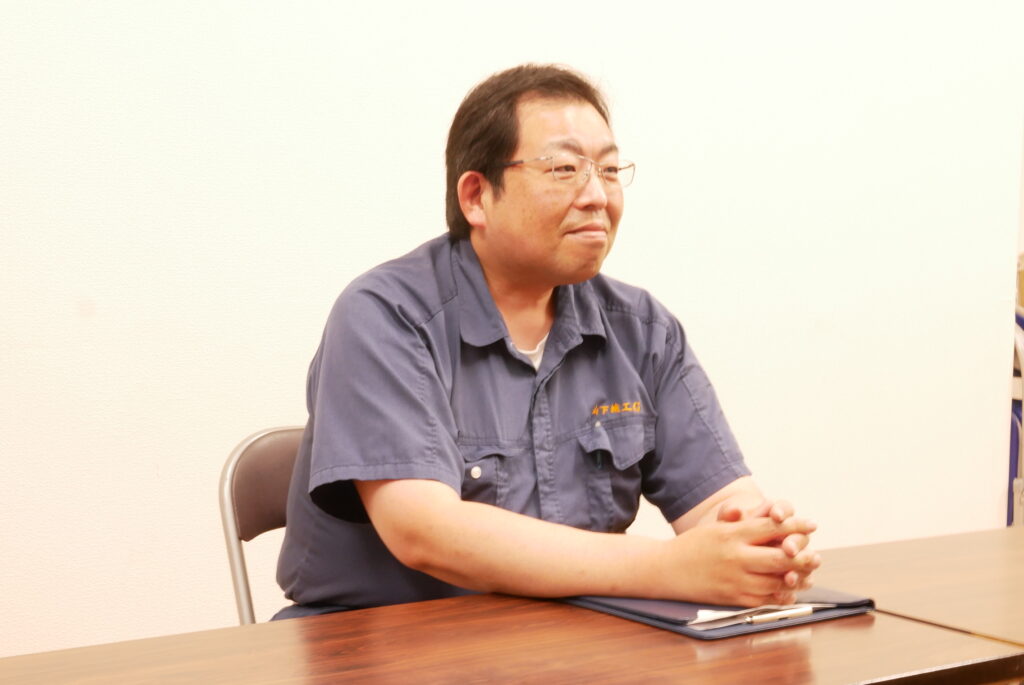
――現在「第4の創業」で様々な事業の改革を進めてらっしゃるそうですね。今回のシステム導入に際しては、どんなお困りごとがあって、どんな体制にシフトしようと構想してらっしゃったのでしょうか?
秋山「現在の社長は3代目。固執した考えはダメ、常に今の世の中で求められていることに対応できないとダメだと考えていて、常々いろんな試みをしています。自社では機械を動かすことで収益を上げる会社ですので、まず、実際にどの機械がどれくらい動いたらどれくらいの収益が上がるのか、現状を知ることが必要でした。効率の見える化です。そのため、5年前に製造過程を全体的に把握できる生産管理システムを導入して物の流れを把握することになりましたが、その一方で稼働データを収集する他社のシステムでは通信や処理データの欠落が頻発し、本当の情報が収集出来ない状況でした。しかし、現状を知らない限り前には進めないと思い、もう1回やり直そうということでお付き合いのある米善機工株式会社さんに相談していたら、KISさんを紹介されました」
――機械の設置にはいろいろな調整が必要だったようですが、導入までにどれくらいの期間がかかりましたか?
秋山「タイトなスケジュールでしたよ(笑)。6月に初めて訪問していただき、導入に向けていろんな調査をしていただきました。当社としては過去に他社で採用した設備のシグナルタワーの光を利用したシステムではなく、設備の使用電流値を把握できるシステムの導入を希望していました。また、事務所や各工場で稼働状況を見られるように65型の大型ディスプレイに映し出すと同時に稼働データを漏らさずに集積する構想がありました。しかし、そういった内容を可能にするには各工場の環境調査と様々な調整が必要だったのです。
結構労力がかかる作業な上に契約になるかどうかもわからないのに、KISさんは「やりましょう」と言ってくれて。
それから電流やネットワークをチェックして環境を整えていきました。そして、これならできるという状況ができて11月に発注したのですが、こちらの都合で納期は年度末。急ピッチで作業を進めることになりました。12月にはクラウド環境を構築し、ハードの制作も開始したのですが、コロナ禍の影響でハードウェア機器が手に入らない状況になってしまうアクシデントも起こり、緊張の連続でしたね(笑)。また、工場が複数あり機械の台数も多くなるのですが、2月に最初の16設備を、3月に残りの27設備に電流センサーパッケージを設置し、無事に実用まで漕ぎ着けることができました」
――実際に使ってみていかがでしたか? 期待していたような効果を感じていらっしゃいますか?
秋山「新しい改善の機会の発見もありました。電流値を測ることで電気代がわかり、古い機械が電気を使うのがよくわかったんです(笑)。家電と同じで古い機械の待機電力が大きくて、これだけの電気を使うなら新しいものに買い替えた方がいいよねと話すようになりました。これは想定外の効果でしたね。
実際に機械のデータを見ていくことで、感覚と現実のギャップがあったことがわかりました。よく動いていると思っていた機械が実はそんなに動いていなかったり、そこまで気にしていなかった機械が意外によく動いていることがわかったり。多品種少量型の生産ですので効率もまちまちではあるのですが、人の動きを見て忙しそうに感じても、実際にものにかかっている時間はそんなにないことも判明しています。データを取ることで今まで知らなかった真実を知ることができましたので、これからデータが蓄積されていくのが楽しみです」
――なるほど。「見える化」することで意外な真実がわかってきたのですね。このデータを活かして今後はどんなことをしていきたいと思っていらっしゃいますか?
秋山「システムを導入すればうまくいくと考えている方もいるかもしれませんが、私は生きたシステムは人の血が通って初めて作られると思っているのです。このシステムを導入して集めたデータ(素材)をどのようにして活かし調理するか」が大事なのです。
このシステムを導入した目的は生産量を増やすことです。生産量を増やすためには作業の効率化が必要で、システム自体は効率化の分析ツールと考えています。まずはデータの集積。1ヶ月、1週間単位で見るとわかることもあるし、1年、2年経って初めて比較できることもあると思います。また、従業員の作業に頼る部分もありますので、作業者の熟練度、例えばベテランと新規採用者などで変化も見られると思います。そういったデータを見ながら何を改善していけば良いかを考え、稼働率を上げていくことにつなげていきたいと思っています。一方で、従業員がデータを取ることで緊張しないように、自然体で仕事に向かえるように配慮することも大事にしたいですね」
――導入前・後のKISのサポートはいかがでしたか?
秋山「ひとつひとつにきちっと回答をいただけたのでものすごく安心感がありました。今までの経験から、アフターフォローをしっかりとやっていただけるところという条件で紹介してもらったのがKISさんです。その言葉に一点の曇りもないです(笑)。特に良かったのは、営業として押し付けてこられなかったこと。営業の話よりも本質的なお話をさせてもらえたのが信頼につながりました。私たちが目的としているものは何かを聞いてくれて、メリット、デメリットを示し、テスト結果の分析も都度報告していただきました。密にやりとりをさせていただき、製造業としての要望、知りたいことを理解していただけたと感じています。こういったやりとりから、KISさんだったら何があっても相談できると思いました。実際、導入した後もしっかりとサポートをいただています」
――ありがとうございます。お互いにしっかりとコミュニケーションをとりながら進めていけたことがよい結果につながったのですね。最後に、秋山さんから見た山下機工さんの今後の可能性についてお話しいただけますか?
秋山「ものづくりを極めたいですね。社是でもあるダーウィンの進化論「唯一生き残ることができるのは、変化できる者である。」のとおり変化を求める社風ですから、常に新しいものを取り入れて常に先を行くものづくりをしていけたらと思っています。ものづくりで培ったノウハウを活かして自社開発品を作って納めるなどできたらいいですね。
それから「人」です。従業員が一番大事。40名の社員はほとんどが地元から採用していますが、その他にベトナムの技能実習生も複数在籍しています。彼らにはベトナムに帰国してもしっかりとしたものづくりが出来るようになって欲しく、日々研修をしています。仕事では日本語で指導していますが、異国の地で3年間頑張ることはすごいなと思って見ています。人は何より大事ですから、入社してきた人を手放さない覚悟を持ちながら、助け合ってやっていきたいと思っています」
今回のシステムは弊社でも初めて扱うものであったことから、導入には細心の注意を払いました。我々はその期間を「実証実験」と呼んでいます。実際にお客様のところへお邪魔して環境を調査し、その条件で機能するかどうか、機能させるためには何をすればいいかを検証して合意形成しながら導入環境を整えました。具体的には、工場のネットワークを無線から有線に変えたり、ネット通信の混雑する時間を調べたり、電流計測の間隔や表示のタイミングを調整するなど、ご要望を伺いながら実際の現場に即したシステムができるように心がけました。こういった時間を重ねることでより充実したものができますし、お客様の目的に寄り添いながら長くサポートしていくことができると考えています。
(左から)SE :菰田景氏、営業:三宅健二、営業:鈴居琴未
今回ご提供したソリューション
設備管理ソリューション:K-EMS1(稼働管理システム)
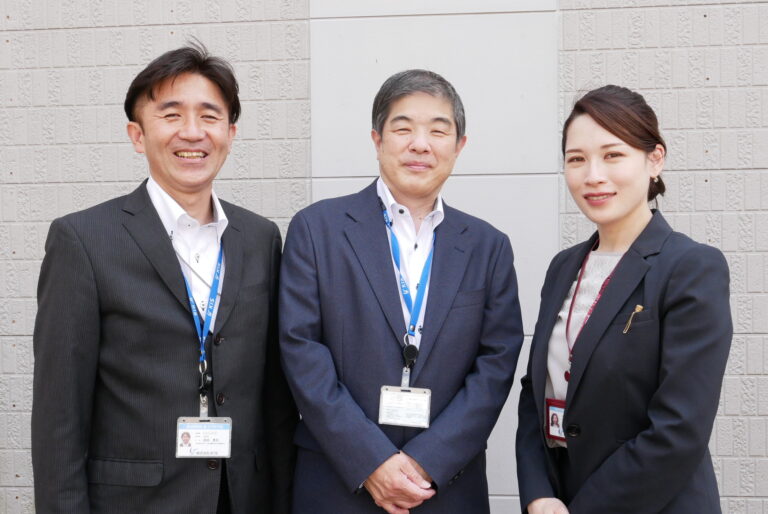
山下機工株式会社
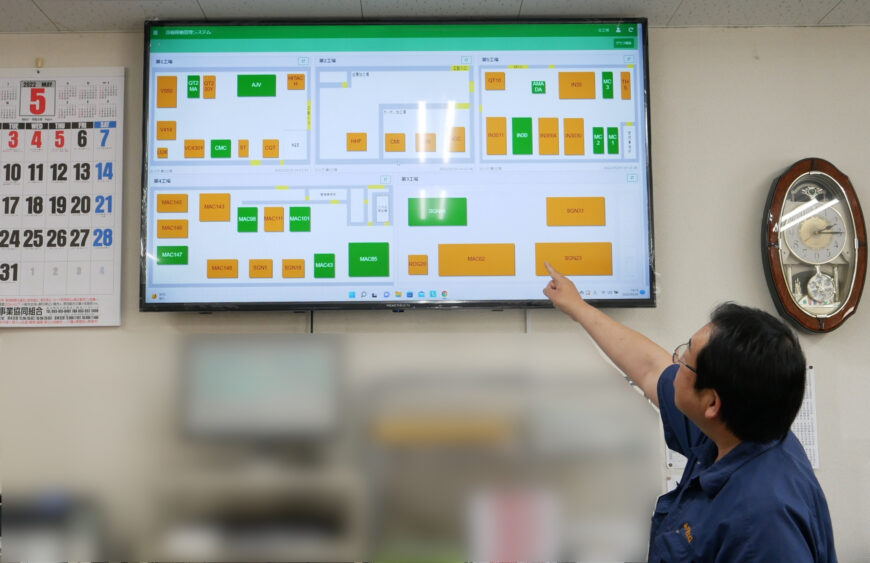